Customer Case Studies
Pickup contents
Industries we serve
News
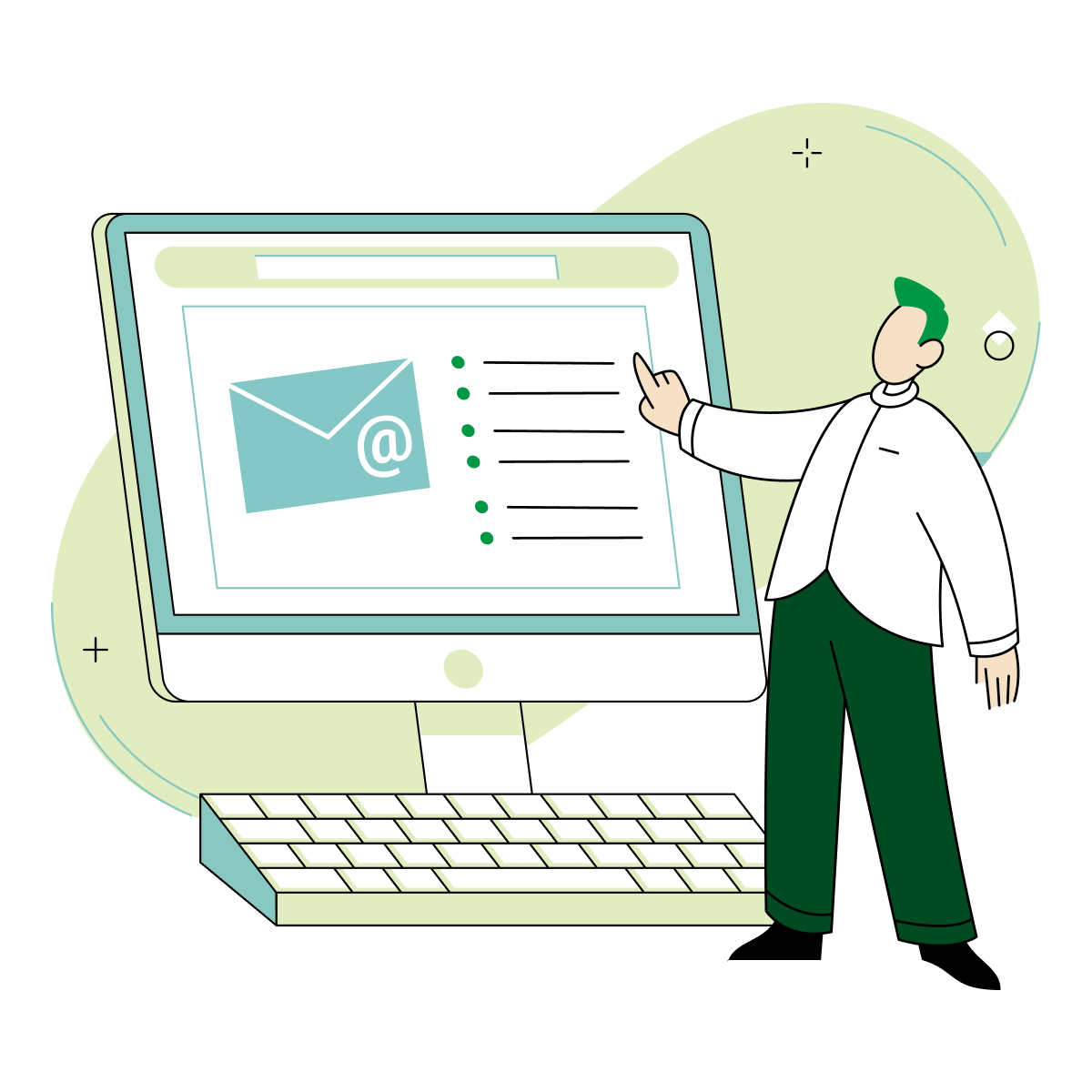
Ready do dive in?
For inquiries about our products and services, or to sign up for a demo, click here.
For inquiries about our products and services, or to sign up for a demo, click here.